In the dynamic and complex landscape of the food industry, where precision, hygiene, and reliability are paramount, bearings stand as unsung heroes, playing a pivotal role in the seamless functioning of machinery and equipment. These unassuming components are vital in various stages of food production, from processing and packaging to transportation. This article aims to explore the crucial significance of bearings in the food industry, highlighting their functions, types, challenges, and advancements.
Bearings are mechanical components designed to enable rotational or linear movement by reducing friction between moving parts. They facilitate the smooth motion of shafts, gears, and other machine components, thereby minimizing wear and tear while enhancing operational efficiency. In the food sector, bearings find extensive application across a spectrum of equipment, such as conveyor systems, mixers, slicers, pumps, and packaging machinery.
Significance in the Food Industry
- Hygiene and Compliance: In food processing, maintaining strict hygiene standards is non-negotiable. Bearings used in the food industry are crafted from materials that comply with FDA (Food and Drug Administration) and USDA (United States Department of Agriculture) regulations. Stainless steel bearings, for instance, are resistant to corrosion and can withstand harsh cleaning chemicals, ensuring compliance with stringent sanitation protocols.
- Contamination Prevention: Bearings prevent contamination by sealing out moisture, dirt, and other impurities. Sealed or shielded bearings equipped with specialized seals and lubricants act as barriers against ingress of food particles or bacteria, safeguarding the integrity and safety of food products.
- Operational Efficiency: Bearings contribute significantly to the overall efficiency of food production lines. By reducing friction, they enable smooth and precise movement, allowing machinery to operate at optimal speeds while consuming less energy. This efficiency translates into higher productivity and reduced downtime.
Types of Bearings Used
Stainless Steel Bearings are renowned for their corrosion resistance and durability, making them an ideal choice for applications across various industries, including food processing.
- Corrosion Resistance: Stainless steel bearings are highly resistant to corrosion caused by moisture, chemicals, and other harsh environmental conditions. This quality makes them particularly suitable for use in food processing equipment, where cleanliness and compliance with strict hygiene standards are crucial.
- Temperature Resistance: They exhibit excellent resistance to extreme temperatures, allowing them to maintain their structural integrity and performance even when exposed to high or low temperatures.
- Hygienic Properties: These bearings are non-porous and easy to clean, meeting regulatory standards set by organizations like the FDA and USDA. They ensure the prevention of contamination in critical industries like food processing.
- Strength and Durability: Stainless steel bearings offer good mechanical strength and durability, ensuring a longer service life compared to standard steel bearings, especially in applications where corrosion resistance is essential.
Ceramic Bearings made from materials like silicon nitride (Si3N4) or zirconium dioxide (ZrO2), possess unique properties that make them suitable for specialized applications requiring high performance in food processing.
- High Hardness and Wear Resistance: Ceramic bearings are extremely hard and exhibit exceptional wear resistance, which contributes to their longevity and reliability, especially in high-speed applications.
- Corrosion Resistance: They are highly resistant to corrosion and chemical attack, making them suitable for use in harsh environments where exposure to corrosive substances is a concern.
- Lightweight and Low Friction: Ceramic materials are lighter than steel, and their low coefficient of friction reduces the amount of energy required for operation, contributing to enhanced efficiency in machinery.
- Temperature Stability: Ceramic bearings can withstand high temperatures without compromising their structural integrity, making them suitable for applications involving extreme heat.
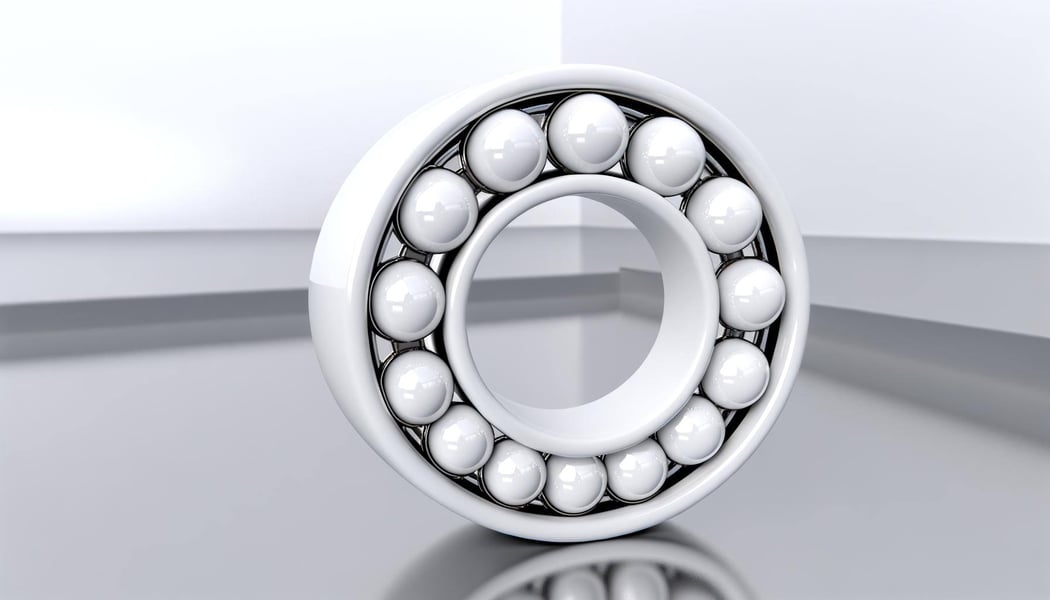
Polymer Bearings are often utilized in conveyor systems, polymer bearings are self-lubricating, corrosion-resistant, and can withstand frequent washdowns without compromising performance. Also known as plastic or composite bearings, they are engineered to offer specific advantages over traditional metal bearings.
- Self-lubrication: Polymer bearings often come with inherent self-lubricating properties, reducing the need for additional lubrication and maintenance in certain applications.
- Corrosion Resistance: They are highly resistant to corrosion, making them suitable for use in environments where exposure to moisture or chemicals is prevalent.
- Lightweight and Dampening Properties: Polymer bearings are lightweight and can offer vibration dampening, reducing noise and enhancing the overall smoothness of operation in machinery.
- Cost-Effectiveness: Polymer bearings can be more cost-effective than some metal alternatives while still providing adequate performance for various applications.
Challenges and Innovations
Despite their critical role, bearings in the food industry face challenges unique to this sector. Exposure to aggressive cleaning agents, extreme temperatures, and high loads can lead to premature wear and failure.
Continuous innovations in bearing design, materials, and manufacturing processes address these challenges, ensuring that bearings used in food processing equipment offer reliability, compliance, and longevity while maintaining operational efficiency in diverse and demanding environments.
- Manufacturers develop bearings with specialized coatings, such as electroless nickel plating or advanced surface treatments, to improve corrosion resistance. Bearings with superior temperature stability and resistance to chemical exposure are designed to withstand extreme operating conditions without compromising performance.
- Innovations in lubrication technology lead to longer-lasting, food-grade lubricants that enhance performance and reduce maintenance requirements.
- Enhanced sealing technologies, including labyrinth seals and advanced lip seals, prevent food particles or bacteria from entering the bearing.
- Continuous advancements in bearing materials, design, and manufacturing processes aim to enhance durability, reliability, and longevity.
Bearings are the unsung heroes silently powering the wheels of the food industry. Their role in ensuring operational efficiency, compliance with stringent regulations, and maintenance of impeccable hygiene standards cannot be overstated. As technology advances, innovations in bearing design and materials continue to elevate their performance, making them indispensable components in the quest for safe, efficient, and high-quality food production.
In essence, the food industry relies on bearings not just to keep machines running but to uphold the trust and safety of consumers by maintaining the integrity of the food production process.
BDS carries a variety of food industry bearings from major manufacturers and with our Class 1000 Clean Room we also have the capabilities to re-lubricate food industry bearings with many different food grade lubricants based on your customers specifications. Visit our website for more information and see what we can do for you.